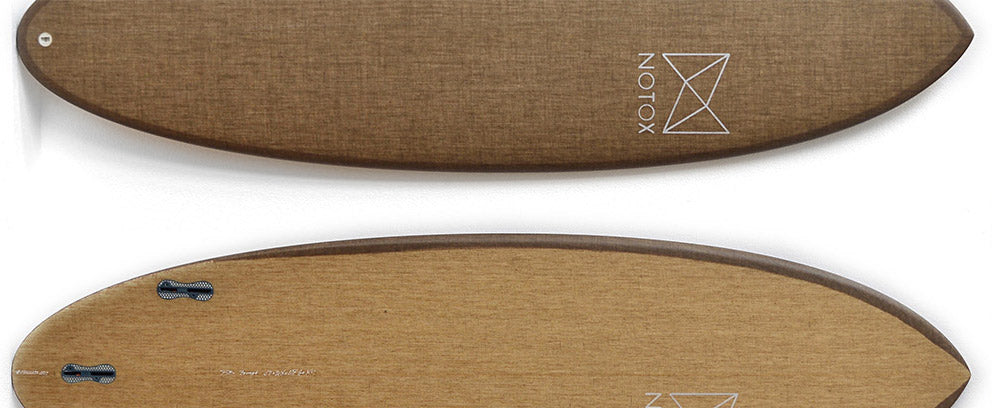
FROM THE ARCHIVE: FLAX COMPOSITES
Image courtesy of NOTOX
Written by Adrian Wilson (Selvedge issue 78)
During the first two weeks of June, the cool blue hue of the flax fields is a welcoming sight in the Plains of Normandy, Northern France. The plant’s slender, delicate stems are set in motion by the gentlest breeze. Linum usitatissimum is an annual plant with narrow, blue-green leaves on 45cm-tall stems apparently only just able to carry the flowers, which are open funnels of sky-blue. This bucolic scene is a world away from high-tech performance composites – or is it?
It is the long fibre from this plant that gives us the porridge-textured cloth once used to clothe medieval monks or to dress the beds in French chateaux, as well as to make crisp, starched napkins used to set a formal dinner table. But there is more to linen than meets the eye. Flax is a food as well as a fibre crop, known for its oil and seeds, sometimes referred to as one of the most powerful plant foods on the planet. Both flaxseed oil and linseed oil are extracted from seeds of the Linum usitatissimum. Flaxseed oil is cold-pressed, pure and has many well documented health benefits; linseed oil is not fit for human consumption, but is instead used as a varnish or polish in wood finishing, as a pigment binder in oil painting and as an ingredient in glazing putty, when mixed with chalk powder. In 1855, the Englishman Frederick Walton saw that solidified linseed oil, backed with burlap or canvas, made a durable floor covering; Linoleum or Lino was born. While the longer fibres are spun into thread the shorter fibres are put to good use in the production of high quality papers, for tea bags and bank notes.
The 32 wind turbines recently erected off the coast of Liverpool, to little fanfare, are each taller than London’s Gherkin tower, at 195 metres from sea level to blade tip. The turbine’s three blades weigh more than 35 tons each and are 80 metres long. This new offshore windfarm is the latest chapter in the ongoing story of the UK’s lead in this renewable energy industry, and will meet the electricity demand of well over 230,000 homes in the Merseyside area. The costs related to such installations are currently dropping through the floor – the potential energy that can be generated by offshore wind installations has doubled in just two years.

Image courtesy of Sylvain Leurent (www.egide-paris.com)
If this appears to be a world away from the traditional production of linen textiles, it’s not. Those wind blades are based primarily on glass fibre and plastic resin composites, and flax has a tremendous and much anticipated opportunity now to replace these glass fibre composites in wind turbine blades, along with many other consumer products such as sporting goods and a host of industrial applications.
So, why exactly is it poised so well to become the next leading composite material? Because flax fibre is hollow, able to absorb 12% of its own weight in water, and its strength increases by 20% when wet.The fibres are twice as strong as those of cotton and five times as strong as those of wool. European flax is known as the best in the world due to the well-suited soil, climate conditions and expertise of the flax growers whose prime concern is quality.
The processes by which the flax plant is transformed into fibre are environmentally friendly. The ‘retting’ of flax – a natural process to break down the outer woody stem making it easier to extract the fibres – consists of leaving the flax in the field, subjecting it to a fine-tuned dosage of sun and rain. This is followed by the centuries-old mechanical processes of ‘scutching’ and ‘hackling’, in which the various elements within the plant are separated, ready for their different uses.
The most obvious example of a naturally occurring composite is wood, while the earliest man-made composites were straw and mud combined to form bricks for building. Composites nowadays are broadly made out of two constituents; either thermoplastic or thermoset resins, and reinforced glass, carbon, aramid or natural fibres. They have a wide range of performance benefits, most notably their very light weight, their high strength and corrosion resistance abilities, which has seen them used as an alternative to steel in many industries.
Founded in 1951, the European Confederation of Flax is a non-profit agro-industry organisation involved in all steps of the production of flax and hemp – from cultivation through to transformation – which to date has primarily been into yarns and linen. Traditional scutching and hackling remain the basis for preparing flax fibres, while fibre ear-marked for composite use does not require further processing. Alternatives that have been developed include random mats and unidirectional and coming led rovings, as well as non-crimp fabrics woven directly from rovings. Each of these have their specific end-uses.

The technical advantages of natural fibre composites lie in their light weight, their mechanical properties (comparable to glass fibres), in what engineers call ‘vibration damping’ (i.e. shock absorption), and insulation ability. This is without taking into account their environmental benefits due to their low carbon footprint along with their biodegradable nature. Nevertheless, as with any new or replacement technology, there is a lot of market uncertainty about its performance properties, and the supply chain has in the past been perceived as both fragmented and reliant to some extent on seasonal conditions. Today, however, the European flax industry is highly organised and vertically integrated. Most companies are involved in at least two or three fibre production processes. Seasonal blends are also cultivated, as well as substantial buffer stock stored. Of the 600,000 tons of flax produced annually in France, close to 28% is long staple fibre suitable for spinning, 50% is short staple fibre suitable for composites, and 10% is powder which has other industrial end-uses. Variety developments an agrotechnology have resulted in vastly improved produce over the past 20 years.
Success stories to date for flax composites have been in the production of sporting goods; snow and surf boards, skis and tennis rackets. Significant vibration reduction, or ‘damping’, has been marketed as a specific performance benefit for both tennis rackets and skis. Ironically, this is the same lack of elasticity that causes linen cloth to crease easily: so what was once perceived as its core limitation, is now flax’s major selling point for the 21st century.
Slow TV, Linen Harvest
Make sure to tune into our upcoming Slow TV experience, a live streaming of the flax harvest at Silverburn Flax Mill.
The date of the Slow TV event can only be predicted a few days ahead of the harvest of the flax crop at Silverburn Flax Mill. Nature defines the harvest and cannot be hurried. We will follow the flax crop during the month of September 2022 to monitor when it is ready to harvest and for the Slow TV event to document the process. Filming is dependent on the flax crop and the weather.
This is a free event that will live streamed on our website on the SLOW TV PAGE.
Written by Adrian Wilson (Selvedge issue 78)
During the first two weeks of June, the cool blue hue of the flax fields is a welcoming sight in the Plains of Normandy, Northern France. The plant’s slender, delicate stems are set in motion by the gentlest breeze. Linum usitatissimum is an annual plant with narrow, blue-green leaves on 45cm-tall stems apparently only just able to carry the flowers, which are open funnels of sky-blue. This bucolic scene is a world away from high-tech performance composites – or is it?
It is the long fibre from this plant that gives us the porridge-textured cloth once used to clothe medieval monks or to dress the beds in French chateaux, as well as to make crisp, starched napkins used to set a formal dinner table. But there is more to linen than meets the eye. Flax is a food as well as a fibre crop, known for its oil and seeds, sometimes referred to as one of the most powerful plant foods on the planet. Both flaxseed oil and linseed oil are extracted from seeds of the Linum usitatissimum. Flaxseed oil is cold-pressed, pure and has many well documented health benefits; linseed oil is not fit for human consumption, but is instead used as a varnish or polish in wood finishing, as a pigment binder in oil painting and as an ingredient in glazing putty, when mixed with chalk powder. In 1855, the Englishman Frederick Walton saw that solidified linseed oil, backed with burlap or canvas, made a durable floor covering; Linoleum or Lino was born. While the longer fibres are spun into thread the shorter fibres are put to good use in the production of high quality papers, for tea bags and bank notes.
The 32 wind turbines recently erected off the coast of Liverpool, to little fanfare, are each taller than London’s Gherkin tower, at 195 metres from sea level to blade tip. The turbine’s three blades weigh more than 35 tons each and are 80 metres long. This new offshore windfarm is the latest chapter in the ongoing story of the UK’s lead in this renewable energy industry, and will meet the electricity demand of well over 230,000 homes in the Merseyside area. The costs related to such installations are currently dropping through the floor – the potential energy that can be generated by offshore wind installations has doubled in just two years.

Image courtesy of Sylvain Leurent (www.egide-paris.com)
If this appears to be a world away from the traditional production of linen textiles, it’s not. Those wind blades are based primarily on glass fibre and plastic resin composites, and flax has a tremendous and much anticipated opportunity now to replace these glass fibre composites in wind turbine blades, along with many other consumer products such as sporting goods and a host of industrial applications.
So, why exactly is it poised so well to become the next leading composite material? Because flax fibre is hollow, able to absorb 12% of its own weight in water, and its strength increases by 20% when wet.The fibres are twice as strong as those of cotton and five times as strong as those of wool. European flax is known as the best in the world due to the well-suited soil, climate conditions and expertise of the flax growers whose prime concern is quality.
The processes by which the flax plant is transformed into fibre are environmentally friendly. The ‘retting’ of flax – a natural process to break down the outer woody stem making it easier to extract the fibres – consists of leaving the flax in the field, subjecting it to a fine-tuned dosage of sun and rain. This is followed by the centuries-old mechanical processes of ‘scutching’ and ‘hackling’, in which the various elements within the plant are separated, ready for their different uses.
The most obvious example of a naturally occurring composite is wood, while the earliest man-made composites were straw and mud combined to form bricks for building. Composites nowadays are broadly made out of two constituents; either thermoplastic or thermoset resins, and reinforced glass, carbon, aramid or natural fibres. They have a wide range of performance benefits, most notably their very light weight, their high strength and corrosion resistance abilities, which has seen them used as an alternative to steel in many industries.
Founded in 1951, the European Confederation of Flax is a non-profit agro-industry organisation involved in all steps of the production of flax and hemp – from cultivation through to transformation – which to date has primarily been into yarns and linen. Traditional scutching and hackling remain the basis for preparing flax fibres, while fibre ear-marked for composite use does not require further processing. Alternatives that have been developed include random mats and unidirectional and coming led rovings, as well as non-crimp fabrics woven directly from rovings. Each of these have their specific end-uses.

The technical advantages of natural fibre composites lie in their light weight, their mechanical properties (comparable to glass fibres), in what engineers call ‘vibration damping’ (i.e. shock absorption), and insulation ability. This is without taking into account their environmental benefits due to their low carbon footprint along with their biodegradable nature. Nevertheless, as with any new or replacement technology, there is a lot of market uncertainty about its performance properties, and the supply chain has in the past been perceived as both fragmented and reliant to some extent on seasonal conditions. Today, however, the European flax industry is highly organised and vertically integrated. Most companies are involved in at least two or three fibre production processes. Seasonal blends are also cultivated, as well as substantial buffer stock stored. Of the 600,000 tons of flax produced annually in France, close to 28% is long staple fibre suitable for spinning, 50% is short staple fibre suitable for composites, and 10% is powder which has other industrial end-uses. Variety developments an agrotechnology have resulted in vastly improved produce over the past 20 years.
Success stories to date for flax composites have been in the production of sporting goods; snow and surf boards, skis and tennis rackets. Significant vibration reduction, or ‘damping’, has been marketed as a specific performance benefit for both tennis rackets and skis. Ironically, this is the same lack of elasticity that causes linen cloth to crease easily: so what was once perceived as its core limitation, is now flax’s major selling point for the 21st century.
Slow TV, Linen Harvest
Make sure to tune into our upcoming Slow TV experience, a live streaming of the flax harvest at Silverburn Flax Mill.
The date of the Slow TV event can only be predicted a few days ahead of the harvest of the flax crop at Silverburn Flax Mill. Nature defines the harvest and cannot be hurried. We will follow the flax crop during the month of September 2022 to monitor when it is ready to harvest and for the Slow TV event to document the process. Filming is dependent on the flax crop and the weather.
This is a free event that will live streamed on our website on the SLOW TV PAGE.