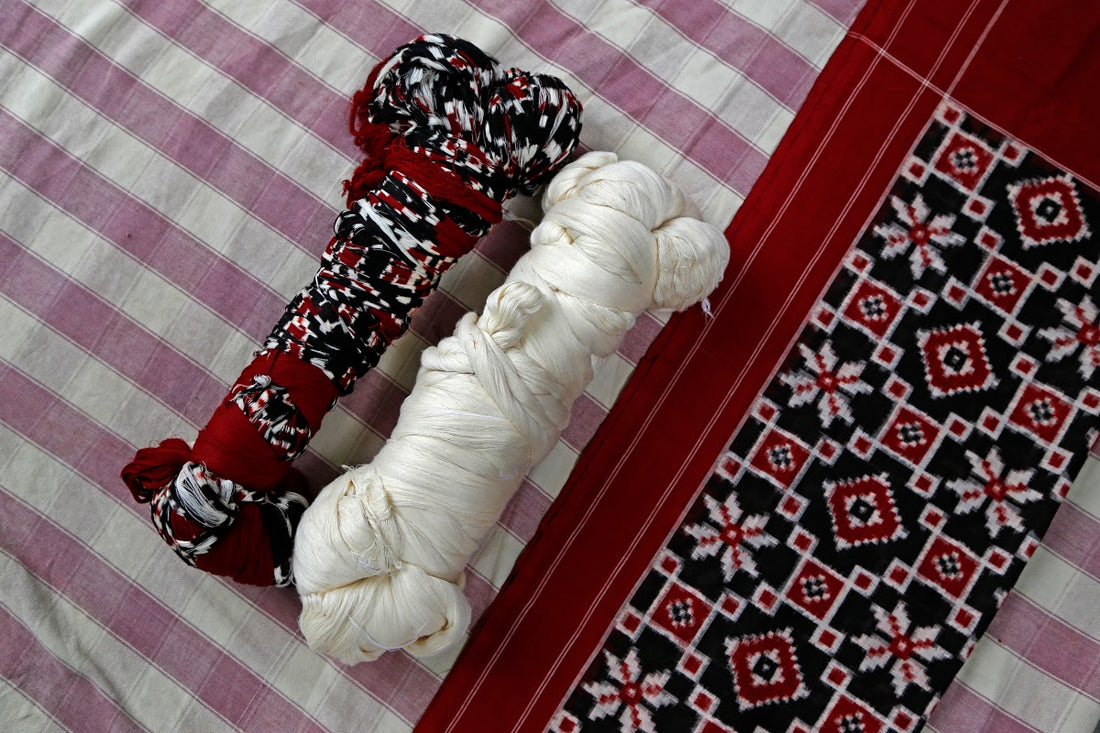
Telia Rumal: From Turban Cloth to Spectacular Saris
Guda Srinu, an award-winning master weaver based in Puttapaka, Telangana state, India, tells us about the weaving of Telia Rumals
“Weaving a Telia Rumal is a skill. From the preparation of the yarns to their resist-dyeing with natural dyes, setting the loom and weaving the yarns carefully to obtain neat motifs, each step requires effort, time, patience and skill. It is like the work of a software engineer. It has to be deliberate and perfect”, says Guda Srinu, 49, a master weaver based in Puttapaka, a village in Nalgonda district, about 60 kms from Hyderabad, Telangana state, India. He aptly makes this comparison as Hyderabad, the state capital, is one of India’s major hubs for the Information Technology industry and is popularly known as “Cyberabad".
A Traditional Textile
The Telia Rumal, is a traditional cotton textile, typically about 45 inches by 45 inches, woven on a pit loom by the meticulous double-ikat technique. The word telia means oily/oiled, and rumal means square or handkerchief, conveying the nature of the textile as square of a slightly oily fragrance that may last for years; this is one of its unique features. This was as traditionally Telia Rumals are woven with cotton yarns that have been processed by repeatedly soaking them in oil before resist-dyeing them.
The traditional colour combination of Telia Rumals is its distinct white, red and black. The traditional Telia Rumal is of a distinctive design featuring a broad, single colour (typically red) border around the field of a grid with squares, and motifs are set within the squares. These motifs are linear/geometric patterns as well as curvilinear and figural motifs like flowers, birds, animals and auspicious symbols. Some Telia Rumals, dated to the first half of the 20th century, have motifs such as clocks and airplanes. Typically the background is black and the grid created by fine white lines. The neat white lines and their intersection indicate the skill of weavers in ensuring the double-ikat pattern/weave is rendered perfectly.
A Unique Textile
Weavers say that the unique processing that the yarns undergo results in the Telia Rumals being durable, soft and comfortable to wear or drape. Further, they say, the oil process makes the yarns receptive to the dyes. This results in the yarns taking on a beautiful brilliant red (when dyed with natural dyes) and a deep saturated black colour (through a natural dyeing process) resulting in a stunning white-red-black colour combination on the woven Telia Rumal. Thus, the Telia Rumal was distinctive for its comfort and beauty of colours and pattern.
“Telia Rumals were exported in large numbers in centuries past to countries in West Asia, the Middle East, East Africa and South-East Asia. When wrapped around the head as a turban, the cloth kept the head comfortable in the heat of summer as well as in the winter cold. Due to this quality, the Telia Rumals were worn by men in desert areas of the state of Rajasthan and by Arabs in the Middle East. They were also precious ritual cloths and heirlooms”.
Reviving the Weave
Guda Srinu has been weaving Telia Rumals for the past twenty-two years. He learnt the technique from national award-winning master weaver Gajam Govardhan, acclaimed for reviving the weave. Govardhanji received the Padma Shri, the fourth-highest civilian award, from the Government of India for his efforts in reviving the Telia Rumal.
The Telia Rumal was traditionally woven in Chirala that is in present day Andhra Pradesh state (the state neighbouring Telangana) and later by weavers in Puttapaka. Telia Rumals were patronized by the Nizams of Hyderabad (who ruled 1724-1948). However, the practise of weaving Telia Rumals declined sometime around the mid-20th century.
Govardhanji, hailing from a family of weavers’ native to Puttapaka, visited Chirala, spoke to old weavers who recollected the technique or mention of it, and after many experiments, iterations and efforts over five years was successful in recreating Telia Rumals. The process involved members of his family and he taught the technique to other weavers in the village, including Guda Srinu. The Telia Rumals woven by Govardhanji and under his direction have been exhibited in India and abroad to immense acclaim. In May 2020 the Telia Rumal of Puttapaka received the Geographical Indications tag.
Yarn Processing
Guda Srinu explains that the unique technique of processing yarns for Telia Rumals stretches over many days. The yarns are first soaked in water for 24 hours and then dried. Then they are washed in a mix of water and sheep/goat dung (obtained locally from the village); three kgs dung is used for washing five kg yarn. The yarn is then beaten on stones/on the floor. This entire process helps to whiten and soften the yarn, and make it absorbent for the dyeing that will follow.
The next step involves burning castor seed pods and obtaining their ash. For five kg yarn, three kgs of ash are taken and mixed in water in a tub, allowed to stand for twelve hours and for the ash to settle, and then the top water is poured into a tub. The yarns are placed in this tub in the open in the morning and it gradually warms up naturally by sunlight falling on it during the day. In the evening, two kg gingelly oil is poured into the tub (amount varies according to the type of yarn) and mixed well; this blend appears like milk.
The yarn is dipped in the solution in the evening, removed in the morning, dried in the shade of a tree, dipped in the solution in the evening and the “morning-evening” process is repeated over twenty days. At the end the yarns become soft and take on a colour of milk. This process gives the yarns the ability to absorb colours very well and in a uniform way.
The Natural Dyes
After the processing of the yarns, the next step involves resist-dyeing of both the weft and the warp yarns according to the design made on a graph. The number of yarns per square inch depends on the thickness of the yarn, and based on this calculation the warp yarns are sectioned and tied accordingly.
While the soft white colour of the yarns is obtained by the processing (as described above), the red and black colours are obtained from natural dyes. For the red colour the yarns are dyed with Indian madder (Rubia cordifolia, Indian name is manjistha); the oil processed yarns take on a bright, durable true red colour due to the oil process. This brilliant, long lasting red colour (that was much sought after especially in centuries past) was one of the highlights of the textile. The deep brownish-black is obtained by soaking iron filings in jaggery water for fifteen days or longer up to 21 for making the solution stronger. The black colour solution is prepared in advance. In some cases, black was obtained by overdyeing blue (from indigo) over the red, in which case the iron filings-jaggery solution was not used.
The Dyeing Process
The yarns are tied and dyed strictly as per the pre-decided design. The length of the warp yarn depends on the number of rumals/stoles/drapes/saris the weaver wishes to weave, and they often stretch out on the warp yarns on the street outside the home for tying them for the resist-dyeing process to follow.
“If we are making saris the yarn is approximately 30 metres long. The length of one sari is 6 metres and the weaver definitely prepares the yarn for at least 5 saris at one time. When it comes to duppatas (drapes) there will be a difference in stretching of the yarn. A single duppata is 2.5 meters long, so for six duppatas fifteen metres of yarn stretching will be done”. The weft yarns are wound on a semi-circular frame with a central peg and a row of pegs along the arc, for tying them according to the design, before resist-dyeing.
The sections of the yarn that are to retain the white (base) colour of the yarn are tied with strips of rubber to resist colour when the yarns are dipped in dyes. The yarns are then dipped in alum solution (mordant for red). Then the areas that need to be red in colour are tied with the rubber bands. Then the yarns are dipped in the iron solution. Then the rubber bands are un-tied from areas that are to be red. Then the yarns are dyed in the madder solution. When they are removed the areas that are to be red take on the red colour, and the areas that are to be dark brown-black have turned black.
The yarns are then washed. The warp and weft yarns are resist-dyed in the same process according to the design. Post resist-dyeing the warp yarns are set on the loom. The tying of the yarn requires precision as does cutting the rubber strips; they have to be cut in suitable length and breadth according to the design.
The Weaving Process
The warp yarns are then set on the loom with the correct tension so that the woven motifs taken on a neat outline when the resist-dyed weft yarns are woven with the resist-dyed warp yarns. Weaving proceeds slowly to ensure the motifs are neat. “The time taken to weave a Telia Rumal depends on the intricacy of the motifs and the number of the motifs. In 2008, Govardhanji and five weavers weaving under his supervision, wove eighteen Telia Rumal masterpieces of 115 inches by 115 inches, with yarns processed the traditional way and dyed in natural dyes.
These Telia Rumals had ten squares by ten squares making a total of hundred squares. The squares had different motifs some of which were complex. These included a horse, lion, lion, different birds (such as the parrot and peacock), tortoise, fish, the traditional game chaupad, different flowers and flowering plants, auspicious symbols. The lowermost right square had the words `Shilpguru Gajam Govardhan Puttapakka’ on a lotus base. These masterpieces are a testimony to the skill of Govardhanji and his guidance to the four/five weavers in recreating the splendour of Telia Rumals. These textiles are now in museums in India and abroad including the Victoria & Albert Museum, London”.
Present Scenario
The scope of Telia Rumals widened as weavers increased the dimensions of the traditional Telia Rumal to weave stoles, dupattas (drapes worn with an Indian dress) and saris. Guda Srinu weaves two to four spectacular saris a month, a few stoles and drapes; the number depends on the intricacy of the design and the thickness of the yarn used for weaving. These weaves are typically marketed by Govardhanji, who assists weavers in marketing their textiles as production per weaver is limited due to time required to weave the textile.
In recent times, Telia Rumal weavers have been facing a difficult time. “It is difficult to obtain castor seeds as local farmers have started growing cotton which is more lucrative. Due to this we are unable to make the ash from castor seed pods that is required for yarn processing. Due to this reason we opt to do away with the processing of yarns in the mix of castor seed ash solution and the oil solution. However, if castor seed pods are provided to us and customers want the traditional oil processed yarns, we can weave the textiles accordingly”.
“However, we continue to dye the yarns with natural dyes, resist-dye the yarns and weave traditional design of a gird with motifs and patterns in the traditional white-red-black colour palette. This colour combination is timeless and is the identity of the weave. Further, if customers ask us to design new motifs or work with different natural dyes such as indigo we do weave such textiles on order.
Guda Srinu, like his mentor Govardhanji, is keen to spread awareness and knowledge of Telia Rumals. “Textile lovers, designers and students visit my home to see and document the craft, and sometimes stay with us. My family members are involved with different aspects of the yarns processing and setting the loom, and two weavers work for me. At exhibitions, I have demonstrated the weaving technique of the Telia Rumal on a sample loom and explained details about the yarn processing and dyeing. Times are not easy with the pandemic, competition from weaves of yarns dyed with synthetic colours and power loom look-alikes. However our weaving of Telia Rumals is our present and future and we are committed to it”.
Contact email for Gudu Srinu is shubhadhayineeg@gmail.com
Text by Brinda Gill, Images Courtesy Guda Srinu
Join Polly Leonard on a once-in-a-lifetime tour of the textiles of India. Find out more information here